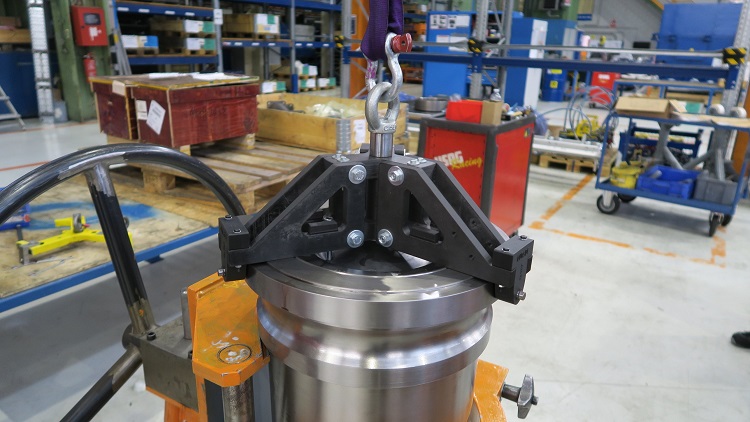
A leading technology group servicing the marine and energy markets – Wärtsilä manufactures the world’s first 3D Printed CE-Certified Lifting Tool
The Challenge
Wärtsilä is a Finland based company that supplies its smart technologies and complete lifecycle solutions to the marine and energy markets. Wärtsilä commands a strong position in all main marine segments as a supplier of highly rated ship machinery and systems. The Finnish factory in Vaasa and Italian factory in Trieste oversee the manufacturing of large engines that power a third of the world’s largest cargo ships. These tools often needed to be fabricated to solve the problems and optimize the performance of both field and factories, before adopting 3D printing technology Wärtsilä has to rely on the third-party supplier to manufacture tools.
One such tool that was very difficult to manufacture for the company was lifting tool. This tool is a custom piece of hardware that empowers them to move immensely heavy engine parts like pistons easily. These lifting tools are significant as they can make lifting operations more efficient during the manufacturing process, and support engineers perform maintenance at the facility or on cargo ships.
Before the adoption of 3D printing technology, Wärtsilä had to manufacture its lifting tools out of solid steel which was a far expensive and time-consuming process. The manufactured part was also too heavy for the people to use and transport. Other drawbacks of traditionally manufacturing the tool were that the team was unable to make quick changes to design when needed.
“The potential to cut costs is really significant. If you’re going to save at least 1,000 Euros per tool, it’s a straight benefit.”
— Juho Raukola Innovation Expert (Additive Manufacturing) Wärtsilä
The Solution
The ultimate solution that engineers at Wärtsilä found was the use of Markforged Industrial Series X7 3D Printer. The engineering team at Wärtsilä had been using Markforged 3D Printing Technology since mid-2018 to make their manufacturing process easier and solve problems associated with manufacturing heavy industrial-grade parts. The Trieste and Vaasa teams at Wärtsilä decided to expand the use of 3D Printing Technology to increase the throughput, so they have purchased a Markforged X7 Industrial 3D Printer for their Italian facility. Working alongside Markforged, engineers at Wärtsilä redesigned the lifting tool for its Industrial Series X7 3D Printer. The new design included splitting the tool into several parts to best leverage continuous carbon fiber reinforcement and enabled the lifting tool to lift a 240-kilogram engine piston on the first try. “I think everybody was pretty shocked about the performance,” said Juho Raukola, Innovation Expert (Additive Manufacturing) at Wärtsilä. The maximum capacity of the 3D printed lifting tool is 960 Kilogram without deformation. The tool has been designed, produced, and tested by Wärtsilä in its premises using the company’s Additive Manufacturing Network. The testing procedure was carried out in collaboration with international certification agency Bureau Veritas, which has granted the tool Type Approval certification which resulted in the world’s first 3D Printed CE-Certified lifting tool.
Adaptation of Markforged 3D Printing Technology by Wärtsilä proved to be a huge success for the company. The company’s estimation shows that they have saved a whopping amount of 100,000 Euro in tooling alone, which they believe can scale with more Markforged 3D printers in more facilities around the world.
Juho and his team are already on the road to freeing themselves from third-party suppliers, meaning they will no longer have to wait for anyone when fabricating tools for their facilities. “We don’t have to work to someone else’s schedule,” said Juho. “And the beauty of 3D printing is that each design can then be printed anywhere at any time through distributed manufacturing, even on the ships Wärtsilä helps to maintain and service.”
“This will enable Wärtsilä to speed up the introduction of new products with faster, cheaper, and safer tool creation.”
— Giuseppe Saragò, Director, Manufacturing Excellence, Wärtsilä
Looking Ahead
With three Markforged carbon fiber printers, and now a Metal X 3D printer capable of printing in metals such as 17-4 PH Stainless Steel, various tool steels like A2, D2, and H13, as well as Inconel 625, Wärtsilä is far from done when it comes to adopting an additive manufacturing approach to solving problems. From tool holders and measuring tools to customer-facing production parts, engineers are now empowered to search for new 3D printed applications all around the production floor. “If we want another tool for production, with specific customer design, it’s not four to six weeks like it was conventionally, but it’s now really a couple of days,” said Giuseppe. “We can answer the need and fulfill the need faster.”