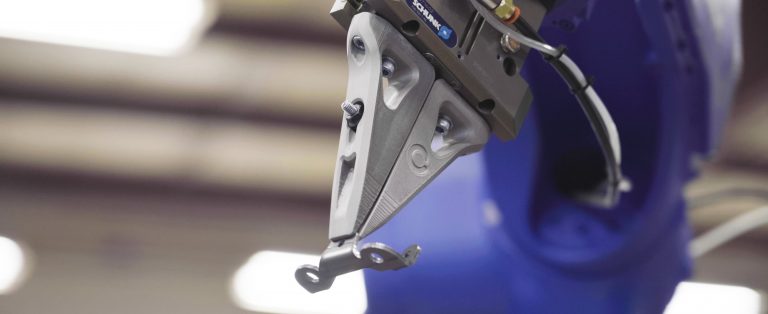
5 Metal 3D Printing Applications That Will Change Manufacturing
Metal 3D printing is a very promising technology, creating great opportunities for the industrial landscape across sectors as diverse as aerospace, manufacturing, automotive, marine, and medical industries. Using this technology, manufacturers can produce fully functioning 3D printed parts with great mechanical properties. As the metal 3D printing is becoming more and more popular, businesses need to gain application-centric intuition about the process. Just as machinists understand which components are best made on a waterjet vs. a 3-axis mill, it is essential to know which parts are a good fit for additive manufacturing and 3D printing applications.
The first step to gaining this intuition is recognizing the fundamental benefits of metal 3D printing. The following advantages are the root of each successful metal 3D printing application.
- Gematric Freedom
Designing and manufacturing of geometrically complex shapes can be hard and expensive with traditional manufacturing techniques. The restriction imposed by traditional manufacturing practices on what can be manufactured is generally not relevant for 3D printing. With metal 3D printing, however, complexity is free. There’s not much metal 3D printing technology can’t do with the proper support material.
- No Tooling
There is no need for expensive tooling and fixtures to hold or secure the parts when making with additive manufacturing. It allows fabricators to create parts with minimal overhead and effort, bringing the cost per part drastically down for low-volume production.
- Automation
Most manufacturing processes require continual human direction to ensure successful outcomes, but that’s not the case with metal 3D printers as it automatically produces parts directly from design files.
With these three benefits in mind, here are five common metal 3D printing applications that are a good fit due to their compatibility with the process.
5 Best Applications for Metal 3D Printing
- Functional Metal Prototype
Metal 3D printing is a great technology for printing metal prototypes as it requires no tooling and less machine set up. It allows you to print metal parts with minimal efforts. With metal 3D printing technology, you can not only achieve creative solutions in engineering and design, but you can also overcome limitations that many of the traditional manufacturing technologies impose.
- End-of-arm tooling
Metal 3D printers can produce conformal end-of-arm tooling much easier and cheaper than traditional methods. 3D printing software automatically generates toolpaths, allowing engineers to skip the CAM process. Additionally, the part complexity of conformal grippers introduces no additional cost, so they can be optimally designed to grip parts securely and precisely.
- Custom Tooling
While most tools are mass-produced, many situations call for specialized instruments that are manufactured in low volumes. Metal additive manufacturing allows engineers to bypass steep overhead and create custom tools at a low cost per part.
- Complex bracketry:
Metal 3D printing offers an alternative way to create intricate brackets that are difficult or impossible to machine. Thin, complex lattices pose no challenge to the 3D printing process, allowing for the inexpensive production of brackets with specialized geometries.
- Low-volume end-use parts
Metal additive manufacturing can remedy high part costs for low-volume production. 3D printers make parts without tooling, getting rid of the need to spread overhead across thousands of parts.