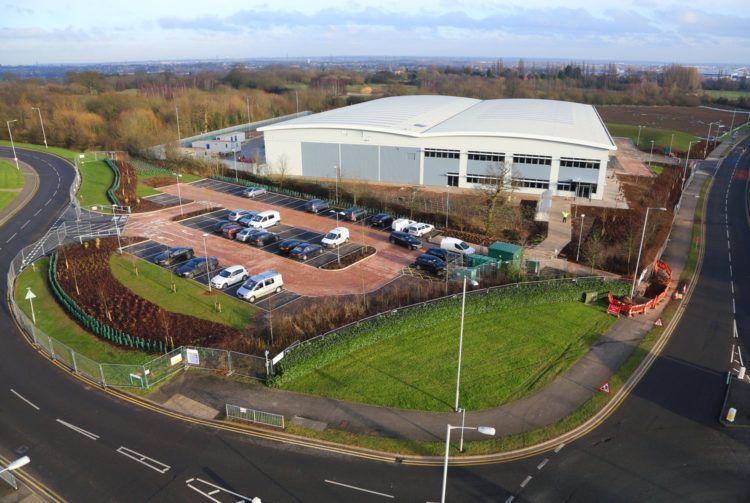
Case study | Dunlop Systems and Components
From Electric Cars to In-House Tooling: How Dunlop is Changing the Game with 3D Printing Technology
The Challenge
Dunlop Systems is a British automotive manufacturer based just outside of Birmingham. The company specializes in Anti-Vibration Solutions including automotive air suspension components and electronic control systems for OEM and aftermarket vehicle applications. Mark Statham, Production Engineering Manager at Dunlop Systems, is in charge of all the tooling used to make Dunlop’s products. The company had a lot of old machinery and in-house tooling that needed to be replaced frequently. Internal and customer tools were sent to a third-party toolmaker to make, however as a result of customer design changes, costs spiralled without being completely recoverable. “You spend all that money and you wait two or three weeks for it to come in, and the customer then phones you up to tell you what they want to be changed,” says Statham. Supplier time constraints was a constant issue, and Mark didn’t want his team to be the bottleneck, so he set about looking for an alternative option.
“I think it’s opened up the mindset. We never say ‘no we can’t do it’, it’s now ‘yes we can.’”
MARK STATHAM,
PRODUCTION ENGINEERING MANAGER, DUNLOP SYSTEMS
THE SOLUTION
Mark attended a seminar about 3D printing where he heard about an industrial-grade 3D printer capable of printing in carbon fiber. He realized he could use it for tooling, as the material was strong enough to withstand corrosive environments. A top-level review of the opportunities outlined during the Markforged seminar took place and as a result, Dunlop Systems completed the purchase of a 3D printer. Since commissioning the 3D printer, the team has found several applications for its use, from prototype parts for electric cars to gauges and moulds. Onyx and continuous carbon fiber have been a perfect fit for the company, providing strong, lightweight parts that can be easily printed on the team’s Markforged desktop printer. “We’re now in the process of replacing, where possible, all our tooling with Onyx,” says Mark. Usually, the department spends around £20,000 on tooling alone. This year, they’re only spending £11,000, thanks to additive manufacturing.